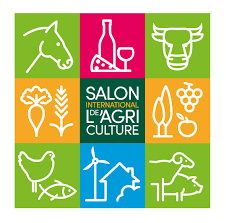
Les savoir-faire
ancestraux
Tanneurs, mégissiers, gantiers, maroquiniers, selliers, chausseurs bottiers : tous perpétuent des gestes transmis de génération en génération pour transformer la matière naturelle. Les professionnels du Pôle Cuir Aveyron sont unis par une même connaissance de leur matériau, par le goût du travail d’orfèvre et de précision, par le sens de la créativité. La finesse de leur production est appréciée par les plus grandes maisons de haute couture. Ils œuvrent tous ensemble à la valorisation et au rayonnement international du « Made in France ».
Tanneurs mégissiers
La peau animale, initialement, est un sous-produit de l’abattoir. Salée sur place pour assurer sa conservation, elle est acheminée en tannerie ou mégisserie où elle va devenir, au terme de plusieurs opérations chimiques et mécaniques, un matériau noble. Les mégissiers travaillent les petites peaux (chèvres, agneaux, peaux exotiques), les tanneurs les grandes peaux (vaches, veaux, taureaux).
En Aveyron, le tannage et le mégissage durent soixante jours. C’est une durée très supérieure au délai minimal requis pour le process. Car comme pour un bon vin, le temps est un allié de l’artisan en quête de finesse et d’excellence.
6
étapes
- En amont, le travail de rivière : il redonne à la peau son humidité naturelle, permet d’éliminer les poils ou la laine, l’épiderme et le tissu sous-cutané, afin de ne conserver que le derme.
- Le tannage, opération charnière qui rend la peau imputrescible, se déroule en trois temps sous agitation continue en foulon.
Phase 1 : le dégraissage élimine les matières grasses naturelles et favorise la pénétration des produits tannants dans le derme de la peau.
Phase 2 : le tannage confère à la peau une couleur gris-bleuté
Phase 3 : après égouttage, essorage et séchage, les peaux sont triées en fonction de leur qualité. - La teinture s’effectue par immersion en foulon dans des bains de colorants.
- Les finitions permettent de donner au produit les qualités spécifiques demandées par le client.
Gantiers
La fabrication des gants de Millau ? Un précieux savoir-faire partagé autrefois par les artisans, les ouvriers et les couturières à domicile, aujourd’hui perpétué avec exigence au sein de manufactures et d’ateliers.
11
étapes
- Le gantier choisit les peaux avec soin. Les gants de Millau sont le plus souvent en peau d’agneau.
- Les peaux sont humidifiées. La mise à l’humide favorise leur souplesse, leur « prêtant », Puis elles sont enroulées, jusqu’à leur séchage.
- D’un geste vigoureux, le gantier étire la peau. Commencent alors le dépeçage et le placage : d’un oeil exercé, le gantier identifie les infimes défauts de la peau.
- Voici l’étavillonnage : une fois mesurés, les gants sont coupés en forme de rectangle ou de trapèze, tout comme les autres pièces : fourchettes et pouces.
- Avec la fente et le découpage, un outil emblématique de la confection gantière entre en jeu : la « main de fer ». Il s’agit d’un emporte-pièce. Les étavillons sont posés sur la main de fer et fendus au moyen d’une presse hydraulique. La peau épouse maintenant la forme de la main.
- Les bords du gant sont égalisés au ciseau : c’est le raffilage.
- La couture commence par la broderie, l’ornementation des pièces : broderies, tressage, entrelacements, incrustations…
- Puis vient l’assemblage du gant. Millau se distingue par son piqué anglais : une technique de couture très rare qui garantit une totale aisance de la main au niveau des entredoigts du gant.
- La pose de la doublure et d’une bandelette de finition parachèvent la phase de la couture. Le gant est alors examiné plutôt deux fois qu’une.
- Après la « main de fer », voici la « main chaude ». Une main d’acier chauffante sur laquelle le gant est dressé et lustré.
- Au terme de leur fabrication, les gants sont appairés.
Maroquiniers
Sacs à main, portefeuilles, ceintures, vêtements… Les maroquiniers réalisent un large éventail de produits d’excellence à partir du cuir, matière résistante et si agréable au toucher.
7
étapes
- Tout commence par le choix du cuir : un cuir fin de bovin, doublé ou non.
- Avec une presse et des emporte-pièces sur mesure, le maroquinier procède au découpage
des composantes cuir du sac (poches, bandoulières, rabat…). - Le cuir, sur certaines sections, est désépaissi au moyen d’une refendeuse, machine réglée au dixième de millimètre.
- Le marquage à chaud du cuir par un embout de laiton permet au fabricant d’apposer son empreinte, son logo, sur le produit.
- Plusieurs pièces du sac peuvent être amincies au moyen d’une pareuse, dans la perspective de la couture.
- Vient l’opération d’assemblage : le piquage à la machine, la pose des rivets, le montage éventuel des fermetures à glissière…
- Le cas échéant, une teinture sur la tranche du sac parachève sa fabrication.
Chausseurs bottiers
Fabrication à la main de chaussures et de bottes souples et robustes, en versions aussi bien rurale qu’urbaine.
7
étapes
- Le chausseur bottier sélectionne le cuir de premier choix.
- Au moyen d’un tranchet, il découpe la peau posée sur une feuille de zinc, en suivant les contours d’un gabarit en carton. C’est la solution manuelle. L’autre solution de découpe consiste à presser, sur le cuir, un emporte-pièce de métal sur mesure, au moyen d’une machine-outil mécanique ou numérique.
- Vient le piquage : la tige est cousue avec une machine à coudre manuelle. La tige ? Le dessus de la chaussure, sa face externe, en cuir souple. L’artisan affine le cuir afin d’éviter les surépaisseurs comme les risques de déchirure. Ses chaussures possèdent deux épaisseurs : le dessus en vache ou vachette, la doublure en veau.
- Place au montage, intégralement à la main. Le cuir de la tige est tendu sur une forme de résine ou de bois (un embauchoir). Ainsi l’artisan obtient le galbe de la chaussure et sa souplesse, ses plis fins et ses replis.
- La finition réside dans l’assemblage de la semelle à la tige, par couture. Une semelle au dessus en cuir et au dessous en cuir ou gomme.
- Selon ses modèles, le chausseur bottier utilise trois techniques : la patine du cuir (contrastes de couleurs), le glaçage (brillance), le satinage (lissage).
- La chaussure est ensuite « bichonnée », autrement dit nettoyée avec soin.
Le CONSEIL NATIONAL DU CUIR propose un guide exhaustif des métiers du cuir.
Selliers
Fabrication artisanale 100% française. Des selles cuir pensées pour le bien-être du cavalier comme du cheval.
9
étapes
- Une fois prises les mesures du cavalier et du cheval, on dessine les plans.
- Les cuirs et peaux sont sélectionnés selon une double exigence de qualité et de souplesse.
- L’arçon, semi-rigide, est préparé. Sur cet élément, qui constitue le siège du cavalier, viennent se fixer les sangles et la matelassure.
- Le cuir est mouillé (plongé dans l’eau chaude). Il s’agit d’assurer la tension du siège en cuir sans qu’aucun pli intempestif n’apparaisse.
- Les composants de la selle sont découpés sur du cuir au moyen d’emporte-pièces ou, à la main, d’un « chasse-peau » et de gabarits.
- Le sellier procède à l’assemblage des pièces (quartiers, faux-quartiers et petits quartiers, matelassures, taquets) pour prendre ses repères en vue de la couture, puis démonte l’ensemble.
- Vient la phase de jointure : la couture des petits quartiers et la pose du siège, l’assemblage des petits quartiers, du jonc et du siège. Puis sont mis en place les quartiers, faux quartiers et sanglons.
- Le jonc arrière est posé : après préparation des panneaux et de leur peau, celle-ci est trempée puis lacée afin que leur tension soit optimale après séchage.
- Le sellier visse et lace les panneaux, procède aux finitions et astique la selle.
Sellerie Auto
Fabrication en atelier de housses qui épousent les mesures exactes des sièges de véhicules.
6
étapes
- Structure, mousse, revêtement : tous les constituants de l’ancien siège auto sont démontés l’un après l’autre.
- Le fabricant procède au traçage des nouvelles pièces : une vingtaine en moyenne pour la réalisation d’un seul siège.
- Il s’attelle à la réparation de la structure de mousse, puis à la découpe de toutes les pièces de revêtement.
- Vient le moment de l’assemblage des pièces une à une, en fonction du type de confection choisi. La durée de l’opération dépend de la forme du siège et du niveau de finitions (surpiqûres, passepoil, piqûre rabattue…).
- Une fois la housse fabriquée, il reste à la solidariser à la structure du siège et procéder à son ajustement afin qu’elle s’adapte le plus parfaitement possible à sa base.
- Dernière étape et non la moindre : le remontage de l’ensemble sur la structure du véhicule.
Restez Connectés
POLE CUIR AVEYRON
CHAMBRE DE COMMERCE ET D’INDUSTRIE
38 Bd. de l’Ayrolle – 12100 MILLAU 05 65 59 59 22
© Pôle Cuir_2021 Mentions Légales